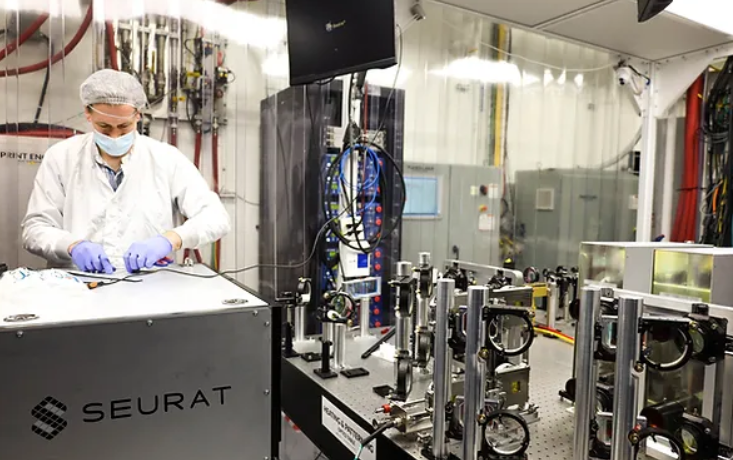
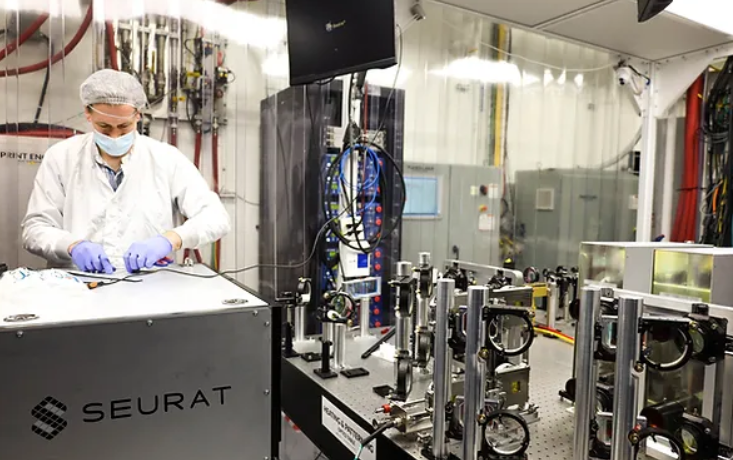
Startup Seurat Technologies Inc., which develops laser-powered 3D printers for the industrial sector, today announced that it has raised $99 million in funding.
Nvidia Corp.’s NVentures fund and Capricorn led the Series C investment. They were joined by about a dozen other backers including the venture capital arms of General Motors Co., Honda Motor Ltd., Porsche AG and Xerox Holdings Corp.
“Our mission is to create a green manufacturing industry,” said Seurat co-founder and Chief Executive Officer James DeMuth. “With our additive manufacturing technology, our print factories will provide our customers with clean manufacturing that can compete with the volumes, quality, and price points of traditional manufacturing.”
Seurat’s 3D printers are designed to manufacture metal products such as wind turbine parts. According to the company, its machines are powered by optical technology that was originally developed at the Lawrence Livermore National Laboratory to support fusion research. Seurat claims that its equipment can produce metal products faster than competing systems and with more fine-grained features.
The starting point of a 3D metal printing project is a container filled with metal powder. The 3D printer focuses a laser beam on the powder, which causes the metal grains to melt and coalesce into a single object. This process is repeated many times to create multiple objects and weld them together into a useful product.
Currently, adoption of the technology is limited because 3D metal printers are fairly slow. A printer generates a single laser beam that can only process a few pounds of metal per hour at most. As a result, the technology doesn’t lend itself too well to large-scaling manufacturing.
Industry players have sought to make their printers faster by equipping them with more laser emitters. The idea is that multiple laser beams can process more metal per hour than a single beam, which in theory leads to faster manufacturing speeds. In practice, however, this arrangement delivers only limited speed improvements.
Seurat has taken a different approach. Instead of using multiple laser beams to create metal products, the company uses a single beam that it splits into numerous smaller rays. Seurat refers to its technology as area manufacturing.
According to the company, the light in its 3D metal printers starts out as an infrared laser beam. This beam is split into about 2.3 million tiny light rays that are organized into a rectangular pattern. Each ray is a pixel in the rectangle.
In the next step of the process, Seurat’s 3D printers tune the 2.3 million tiny light beams to melt metal into a specific shape. This tuning is done by combining the infrared laser light with blue light. The task is carried out using a device called an OALV, or optically addressed light valve, that was developed at Lawrence Livermore to support the construction of fusion reactors.
Seurat says its technology is a more capable alternative to other 3D metal printing methods. By next year, the company expects that its printers will be capable of manufacturing metal products with a feature size of 100 microns. It says rival manufacturing methods can reach a range of only 150 to 2,000 microns.
Feature size is a metric that influences the level of detail a 3D printer can achieve when creating metal products. The smaller the feature size, the more advanced the printer. As a result, Seurat’s approach theoretically makes it possible to create more sophisticated products than other manufacturing techniques.
The company expects its hardware to improve significantly over time. Seurat plans to decrease its 3D printing feature size from 100 microns to 75 by 2027. In the same time frame, the company hopes to build printers that can produce 66 pounds of metal products per hour, which is several times more than what current systems support.
Seurat expects even more significant improvements to materialize next decade. Beyond 2030, the company believes, its technology could be used to build printers that can produce 3,700 pounds’ worth of metal products per hour.
Seurat is currently setting up a pilot factory in the Boston area that will be dedicated entirely to 3D metal printing. The company deployed its first printer at the facility earlier this year. According to Seurat, the proceeds from the funding round it announced today will be used to install additional machines and increase production capacity.
Seurat’s technology is drawing significant industry interest. In the coming years, Siemens Energy AG plans to work with the company to print 59 tons of wind turbine components. Additionally, Seurat has secured letters of understanding for potential manufacturing deals that it says could be worth $750 million.
The company’s long-term plan is to set up a network of 3D metal printing facilities around the world. Those facilities will be located at or near customers’ factories to simplify logistics. Because its printers are powered by renewable energy, Seurat estimates its plants could avoid up to 100 million tons of CO2 emissions by 2030.
THANK YOU