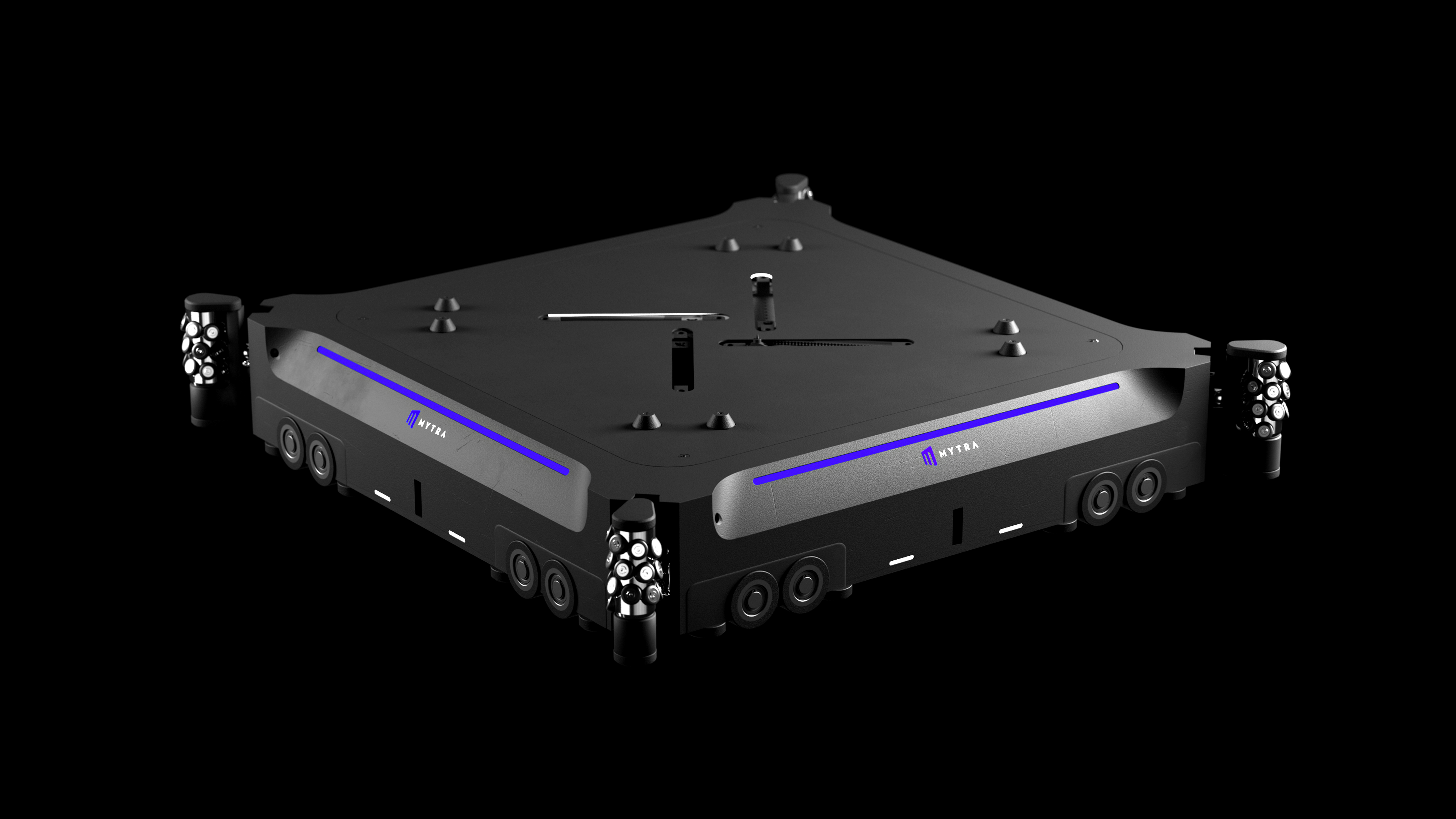
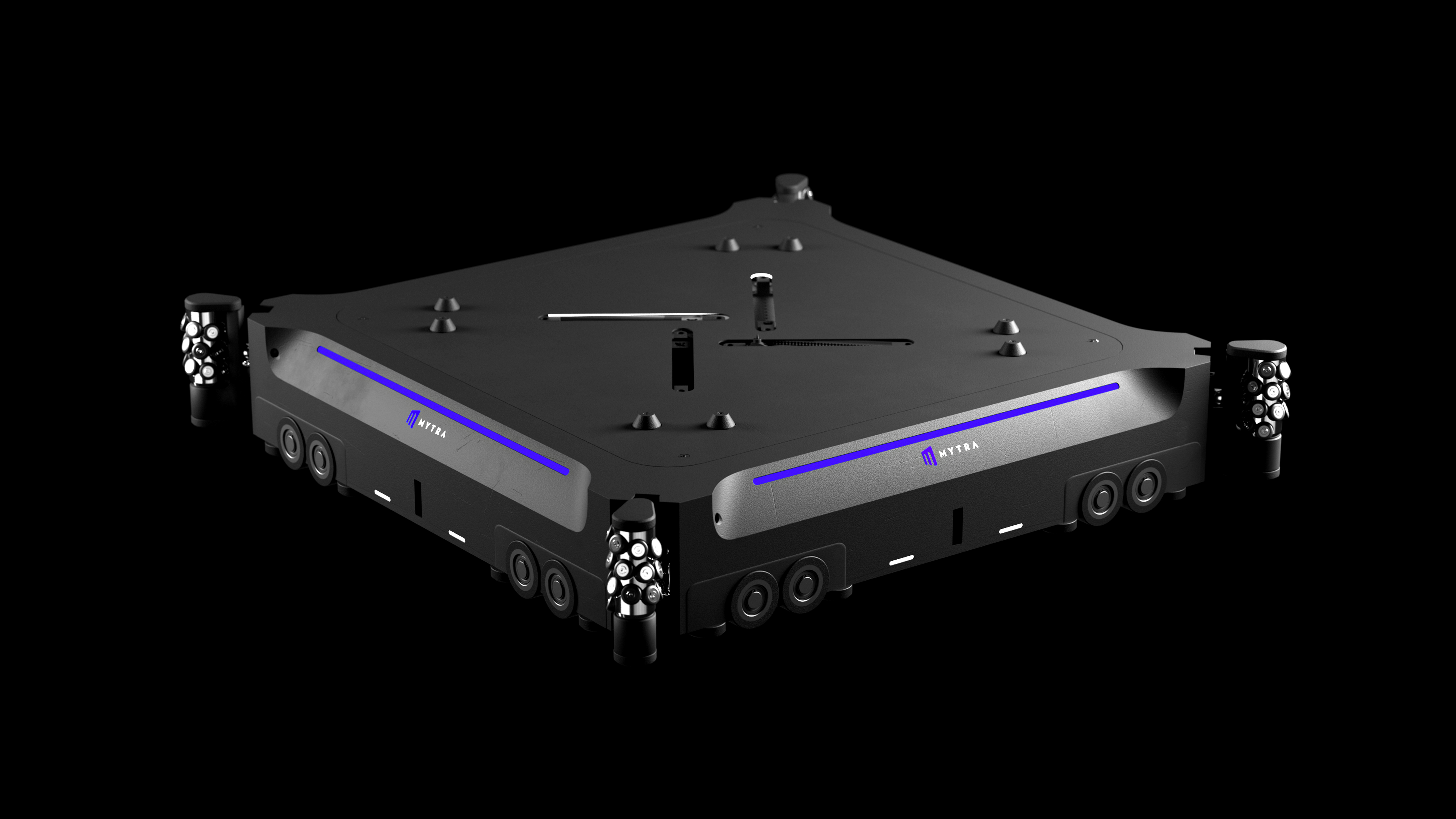
Mytra, a warehouse automation solution that uses artificial intelligence and robotics to move materials, today announced its launch from stealth with a total of $78 million to solve the biggest problems facing physical storage right now, which is moving materials.
The company has developed a novel solution for storing and moving materials in a three-dimensional grid, making the best possible use of space. The matrix lattice for the storage grid can be built quickly and easily from simple, modular pieces of hardware, which takes a lot of the technical debt off the customer and it can be shaped to fit whatever space customers have.
The company is backed by Greenoaks, which led the company’s Series B funding round and Eclipse, which led the company’s Series A and seed funding rounds, in addition to Okta Inc. co-founder and Chairman Frederic Kerrest’s 515 Ventures and others.
Mytra’s robot works like a pallet jack and can move within the 3D lattice structure to pick up and drop off boxes within different cells. Using rollers and grippers on its sides, it can roll side to side or move vertically either unloaded or with a box atop its square holding surface. That means the robot can move wherever it needs through the lattice and pick up and move items, and warehouse administrators can choose how to configure where items are stored.
In an interview with SiliconANGLE, Mytra co-founder and Chief Executive Chris Walti, a former manager for Tesla Inc. robots, said that he founded the company to help disrupt the highly specialized industry of logistics behind what is called “material flow.” That’s the delivery of product between different parts of manufacturing processes or from packaging to staging or within retail warehouses to display.
“You see all sorts of bespoke, customized and custom things, conveyors that are moving boxes and pallets from a very specific point to another specific point,” said Walti. “And you know what should sound alarm bells in your head is like, wow, that is a lot of tech debt. That is a lot of stuff to maintain, that’s a lot of stuff to install. It’s a lot of stuff to configure. There’s literally thousands of different unique parts that are needed to make all this happen.”
What’s worse, Walti pointed out, is that if a business changes, the material flow might also change and all those conveyors, custom setups, sensors and the like need to be changed. That could be an undertaking that would cost a business millions of dollars from the outset and an investment that might be so prohibitive that it could make it impractical to change it and thus catch up with a business opportunity.
Mytra’s robots can move up to 3,000 pounds horizontally and vertically through the matrix cells. The company’s name comes from a Greek word, “Mitra,” which means matrix. When moving between cells, robots will avoid each other and administrators can define clear corridors as hallways and columns and elevators for them to move boxes through. This allows them to easily define where robots can store and retrieve items, creating regions within the matrix for storage.
The robots are “highly collaborative,” Walti explained, because of the environment and the space within which they need to operate. Any given storage matrix is expected to support more than one bot at a time and they will be moving to retrieve and deliver objects from within the lattice with other bots all the time at very high speed. So they have artificial intelligence algorithms that help them avoid collision and lock states that might create traffic jams or unemotionally trap a bot within a section of the matrix.
“It’s unique to our problem that we have to solve, and it enables these bots to become, very independent thinking agents in a very high velocity and high concentrated environment,” Walti said. “Think of ‘Minority Report’ where all those vehicles were spinning around in a very dense city, living in all different axes. Like these bots will be able to do that in full three dimensions. Humans are pretty darn good at doing this too. Walk down the streets in New York, and people, surprisingly, don’t run into each other that often.”
Walti’s experience comes from working at Tesla, the company best known for its autonomous cars – and now also for its work on the Optimus humanoid robot. His early work there involved working with a team scaling up an autonomous robot that could move in all directions and carry heavy loads. Eventually he was put on the humanoid robot team but felt like that wasn’t where he wanted to put his efforts, so he left the company.
According to Walti, warehouse and manufacturing centers need to solve practical problems such as material flow issues and Mytra’s solution does exactly that. Although humanoid robots and other manipulators have an interesting niche use case, they’re not quite there yet.
“Just moving stuff around is the most valuable problem. We really wanted to attack this in a way that has never been done before,” said Walti. “If we can pull this off, there’s 250,000 warehouses around the world. It’s denser [than current solutions] and very cost-effective. It’s deeply useful, highly versatile, and that’s why we decided to spend our time here and not on more buzzy robotics.”
THANK YOU