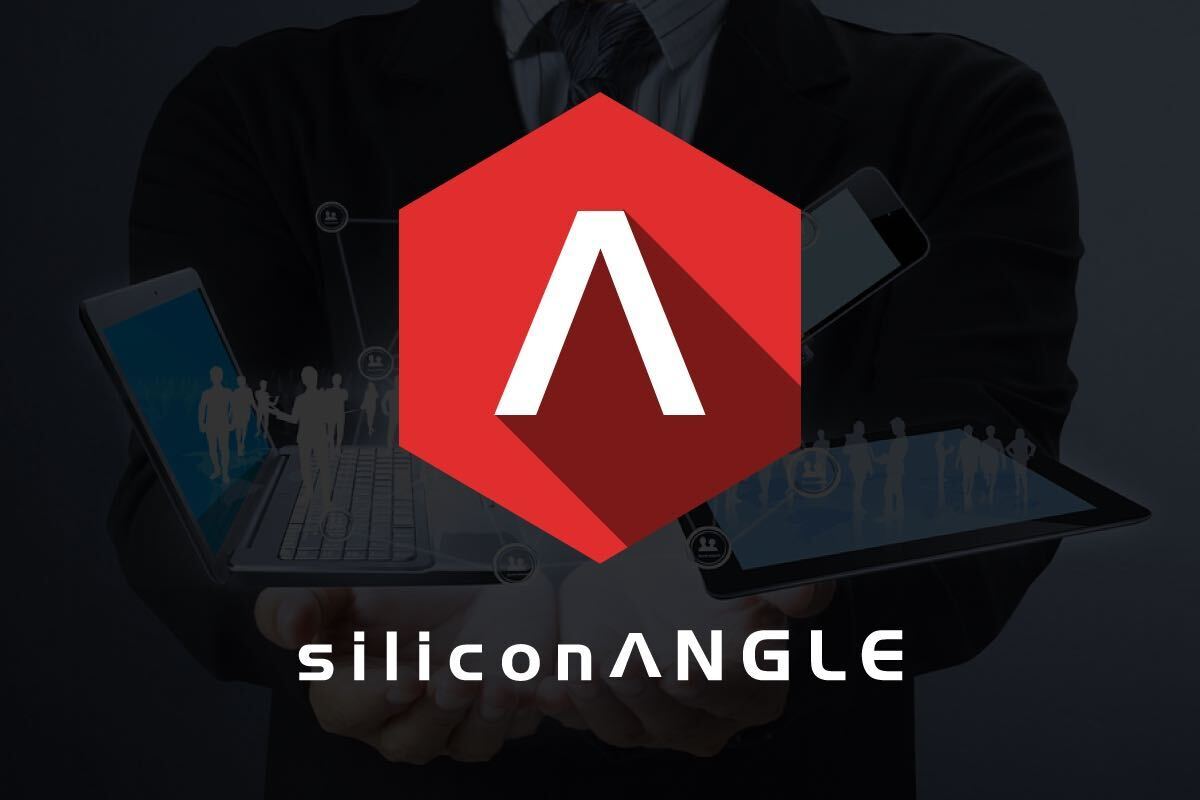
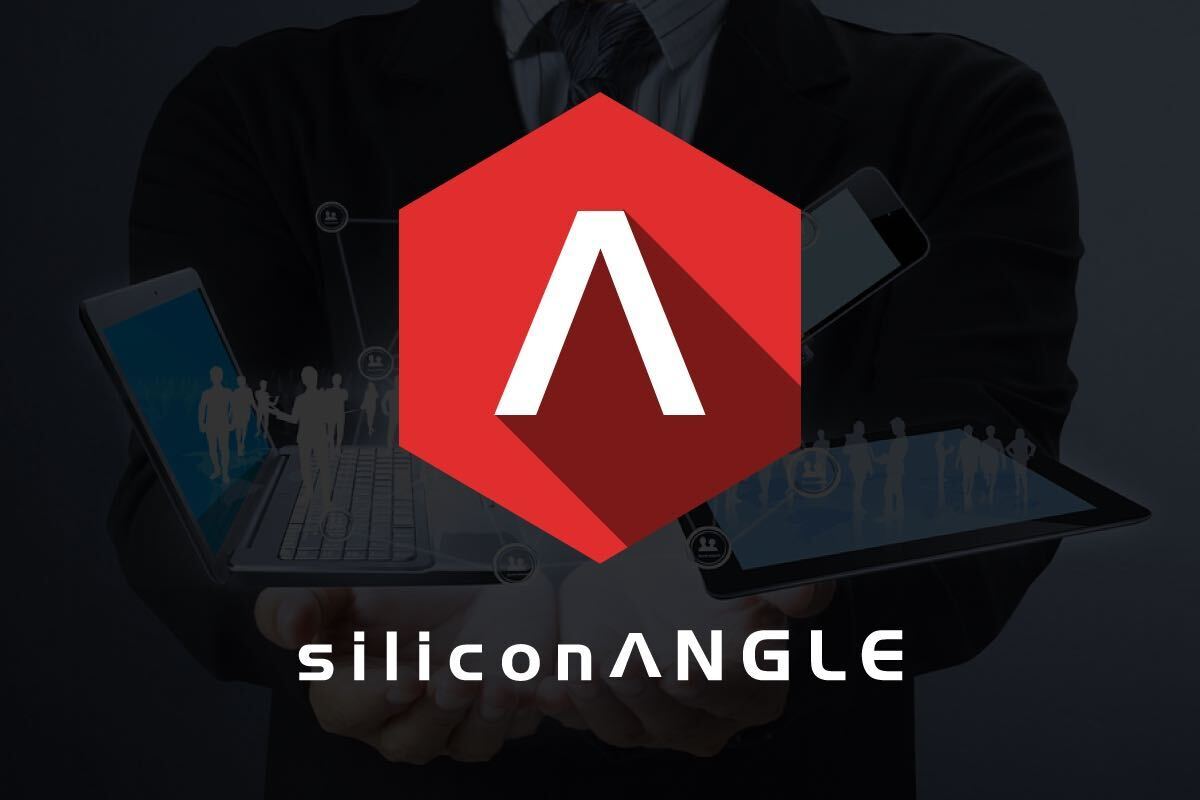
Over the course of four days, the IBM Pulse 2014 Conference brought the attendees hundreds of sessions that aimed to demonstrate how to apply the right tools and the right technologies to help the organizations achieve limitless possibilities in the cloud.
The “Building a Smarter Infrastructure“ keynote reunited on stage George Ahn – Vice President of Smarter Infrastructure, Hugo Beltran – Associate Chief Engineer with Honda North America, Pete Karns – Director of Product Strategy with Smarter Infrastructure and Stewart Gibbins – Director of Operations with Infinis.
First to take the stage, Ahn needed to clarify that “2013 was a great year for IBM,” as the company has made some substantial and significant investments in smarter infrastructure. And IBM clients also made substantial investments to move their infrastructure forward. Out of hundreds of possible examples to choose from, Ahn used the city of Boston as his case study, sharing GSA’s story.
“At GSA they have over 350 million square feet of real estate and facilities in their management and 8,000+ buildings; their first project was to manage their infrastructure, facilities and real estate, reducing energy costs. They did that with 33 million square feet and it was a success,” said Ahn.
As for the city of Boston, they had various areas that needed corrective actions (Maximal, Tririga), and those led to significant savings.
Taking the audience back to last year’s Pulse edition, Ahn recounted:
“Last year we talked about three things:
1. the explosion of data – The convergence between the physical and the digital world
2. how the engagement model with the mobility is changing
3. and how the complexity of our world is continuing to get more and more complex.”
Ahn noted that the workflow is changing. Using Maximal, the city of Boston managed a preventive maintenance on 60,000 street lights, resulting in a huge cost savings.
.
The increasing complexity of the current world is amazing. To stay relevant, IBM had several notable investments. Talking about the mobility solutions, Ahn highlighted:
“Many of you are running on-premise Maximal solutions; inventory insights is available to you in the cloud. This is really analytics in the cloud. It will make the integration between the cloud and the on-premise as seamless as possible. This would drive the cost of deployment down but also significantly improve your time to value.”
After specifying that IBM has moved the core capabilities of Maximal to “as a Service,” creating the Capability as a Service, Ahn surrendered the stage to Beltran.
“We are taking a mobile journey at Honda and it’s leading us to a pro-active culture,” began Beltran. “Before I start, let me offer a background of what Honda does: we build automobiles, we’re a mobility manufacturing company, we make motorcycles, ATVs, generators, marine components; we’re into racing, we make robotics, we make walk-assist for the disabled and the elderly and we’re expanding into aeronautics with the Honda Jet.”
He continued: “Some of these products are produced locally here in North-America. We have 15 facilities, and we just started a brand new one in Mexico. Since we started production in our 15 facilities, we’ve produced 20 million cars. If you put them end-to-end, you can loop around the globe twice.”
Walking the audience through the Honda philosophy, Beltran explained: “The Genba (the focus) is always changing. Our executives and associates are motivated to drive and improve it everyday, to make Honda more efficient. If the drive and engagement is not properly focused, we can go different directions. My sole responsibility is to coordinate all the initiatives to focus like a laser beam to enhance Honda and to continue to move forward.”
.
In Beltran’s words, the Honda vision is “to achieve and sustain high efficiency production,” and for that they have three pillars:
1. Increase Equipment Reliability
2. Increase Floor Skill Level
3. Improve Management Systems
Their goal is to have a pro-active culture. An important key initiative was introducing mobility into manufacturing environment, achieving 30 percent faster production.
Beltran presentation described the old way of conducting business versus the new one.
.
1. Machine failure generates alarm
2. PLC triggers alert in ActivPlant
3. ActivPlant collects and stores incident data
4. Enterprise Gateway evaluates incident against rules
5. IBM Maximo creates work order based on EG rules
6. IBM Maximo creates PMs based on work orders
7. Maintenance technician reviews PM list
8. Maintenance technician completes PM
NEW
.
1. Machine failure generates alarm
2. PLC triggers alert in ActivPlant
3. ActivPlant collects and stores incident data
4. EXT7000 evaluates ActivPlant incident against rules
5. EXT7000 sends alert to mobile and technician creates WO
6. IBM Maximo creates work order based on EG rules
7. Maintenance technician manages WO, parts and history
8. Maintenance technician completes PM
9. Maintenance technician closes WO
Honda’s goal is to have no production downtime, and the team feels empowered by having a new tool on their belt.
Next on stage, IBM’s Karns stated that “clearly Honda is making moves that matter, using data to fuel analytics and mobility to enable process optimization.”
Referring to other clients, Karns specified that there are 1) clients across a whole range of industries who continue to make investments to manage risks, manage complexity and lower costs and 2) clients who make new types of investments, designed to transform the way infrastructure, products and devices are managed – “not only to manage costs, but to grow revenue and differentiation, to innovate.”
Pete Karns mentioned three disruptive technologies: mobility, analytics and cloud.
Mobility
“Last year we released our next gen mobile platform, called Anywhere – it is built on IBM’s Mobile Enterprise Application Platform and it was designed to: access information and capabilities right at the point of performance (in the field, in the facility or in the plant). In addition to that we took an evolutionary step forward with work planning, scheduling and dispatching, adding an algorithmic based engine, an optimization engine, with pre-built models, to enable you to get the right skills to the right job, at the right time, in the most efficient manner possible.”
Analytics
“Our goal is to address a range of requirements seen from you – there’s predictivity, prescriptive type analytics. We offer free downloadable content packs for business intelligence for Maximal. These will help you gain increasing insight into your operations.”
Cloud & the hybrid SaaS model
“Another aspect of our investment in the cloud is beginning to introduce our core Capabilities as a Service.”
“We’ve accelerated your ability to achieve a smarter infrastructure,” declared Pete Karns before leaving the stage to Gibbins, who shares the story of his company.
“Infinis was formed in 2006 and since that time it became the UK’s largest independent renewable generator, producing some two and a half terawatt hours of electricity, sufficient to power 1.2 million homes,” stated Gibbins.
“The majority of that electricity comes from our 121 by gas power plants that utilize landfill gas to generate base load electricity. The challenge for Infinis was how to maintain and operate 147 power plants which were un-staffed, and geographically dispersed across England, Scotland, Wales and Northern Ireland. Infinis has to collect sufficient volume of landfill gas to fill an Olympic size swimming pool every minute. Landfill gases contain large amounts of contaminants and that causes wear in our reciprocating engines. The gas on every site can be different. Some sites have a high acid content which will attack the iron components in the engines; this means we need to change and optimize maintenance schedule for each individual site to get the best possible performance out of the plant. To optimize logistics, 24/7 logistic center was built using Maximo at the center of their management system, coupled with a real-time supervisory control ,” explained Gibbins.
The Infinis Critical Performance Goals are:
• Improving equipment maintenance to extend mean time between failures (MTBF)
• Accelerating repair response to reduce mean time to repair (MTTR)
Make sure you watch the entire segment and the Panel Discussion
below:
THANK YOU