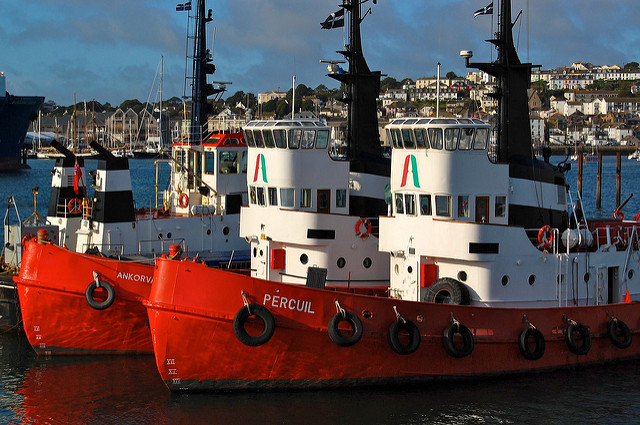
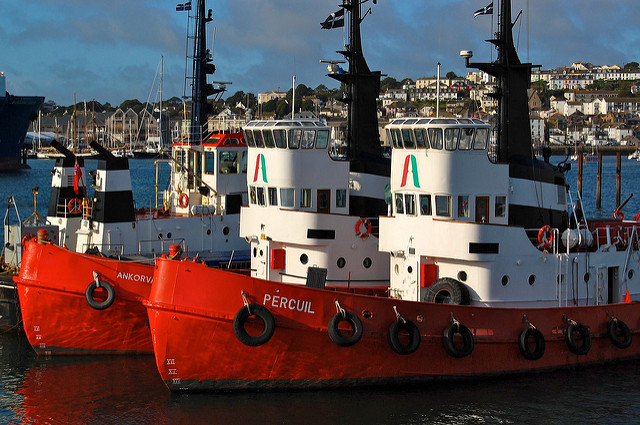
This is a sponsored post commissioned by Pentaho Corp. Sponsor Posts are paid posts that appear on all pages of SiliconANGLE.com, supporting editorial efforts. For pricing and inquiries, email sponsor@siliconangle.com.
Tugboats, barges, ferries and other water-bound workhorses are the bread and butter of the shipping industry. Often running nearly round-the-clock, they are thinly staffed and tightly scheduled. Some tugboats run with just a single operator. Yet these boats are like miniature cities when it comes to the variety and complexity of equipment they house. In addition to the diesel engines that power propulsion, working boats may contain air and water purifier, chillers, heating and air-conditioning units, thrusters, steering units, oily water separators, controllable pitch propellers, pumps and navigation equipment. All of it operates under harsh weather conditions with corrosion from salt and spray thrown into the mix.
And sometimes machines break.
That’s where Caterpillar Marine’s data analytics service comes in. The subsidiary of the well-known yellow-tractor company sells fuel propulsion systems, auxiliary marine engines, treatment solutions and fuel gas handling systems to a wide variety of industrial fleet owners. Now it also uses big data and predictive analytics, powered by software from Pentaho, to help its customers manage their water-borne assets more efficiently.
The technology was developed by ESRG Technologies Group, LLC, a 15-year-old vessel monitoring and data analytics company that Caterpillar Marine acquired last year. Staffed mostly by retired navy seamen, ESRG developed software that translates maintenance data into operational recommendations that help customers wring more life out of their machines and keep their boats on the water longer.
ESRG was in the “Internet of things” business before it was fashionable. Using sensors embedded in or attached to on-board equipment, the company’s technolog
y listens for signs of impending malfunctions, such as changes in pressure, temperature or engine speed.
By predicting that machinery is about to fail, Caterpillar Marine enables its customers – who are mostly fleet owners – to schedule maintenance during planned downtime and avoid the nightmare scenario of having a working vessel suddenly go dead in the water.
Unplanned downtime can be disastrous in the low-margin shipping business, particularly for small fleet owners whose vessels haul cargo or nudge large transport ships through small spaces. Tight schedules don’t provide latitude for delay: if a tugboat isn’t there when the customer needs it, someone else quickly gets the business.
CAT® Connect provides both on-board detection and sophisticated predictive analytics. It replaces alarm systems – which tend to fire off only after the damage has already been done – with intelligence that anticipates problems in time for ship owners to fix them.
Caterpillar Marine’s technology acquires, manipulates, cleanses and qualifies data at an average sampling rate of once per second and up to 20,000 times per second in some instances, according to Jim Stascavage, Marine Asset Intelligence Technology Manager at Caterpillar Marine.
“We identify trends toward failure before they become alerts,” he said. For example, a decline in oil pressure may not trigger an alert if the pressure is still within the normal operating range. However, the trend may indicate that a failure is imminent. Knowing that fact enables the operator to act before equipment fails. “The deviation won’t trigger an alarm, but it should, because the trend is starting to go in the wrong direction,” Stascavage said.
For customers, payback is often immediate. For example, using trending information to predict the failure of a single fuel pump saved one Caterpillar Marine customer $35,000 in annual maintenance costs and reduced the risk of customer loss due to downtime.
Fuel pumps were dying every two to three months on board the company’s fleet of tugboats. Analysis showed that pump pressures began to decline about seven days before failure and that the decline accelerated again three days later. Because the pattern was predictable, Caterpillar Marine recommended a replacement schedule based on sensor data that eliminated vessel downtime. “This was low-hanging fruit, and an instant return on the customer’s investment,” Stascavage said.
There’s an even bigger potential payoff when large volumes of data can be analyzed and combined to uncover trends that point to bigger cost-saving opportunities. So every 15 minutes, Caterpillar Marine’s onboard system rounds up the data it’s collected and transmits it to shore for deeper analysis.
“We want customers to see things that are important to them that might not be easy for them to view just with our on-board software,” Stascavage said. That’s where Pentaho comes in.
Pentaho’s integration and analytics products harmonize data from a wide variety of source formats and enable analysts to construct complex models to detect relationships humans can’t see.
Data integration and transformation is one of the important benefits of the Pentaho solution. Data streams in from ships in dozens of formats – such as temperature, pressure, RPMs, geographic coordinates and geometric angles – which vary by industry standards and manufacturer specifications. “We’re mashing all this data together and trying to figure out what it means for the performance of the ship,” Stascavage said. “It’s not simple for even one ship, so you can imagine how complex it is across an enterprise. There are literally trillions of data points that need to be evaluated every year.”
Caterpillar Marine developers could have written their own filters, but that would have distracted them from their more valuable analytics work. “We wanted to put data in a common format so our software wouldn’t have to deal with transformations,” Stascavage said. “The company had already bought into Pentaho, so we decided to use that.”
Pentaho Data Integration uses a metadata-driven approach and a graphical drag-and-drop design interface to simplify a complex data transformation procedure called extract/transform/load (ETL). It provides a scalable approach to harmonizing data in different formats and loading it into the company’s open source analytics and reporting tools.
Once data is in a common format, analysts can use visualization and multidimensional cubes to correlate many variables and identify relationships. For example, a cube could combine data about fuel consumption, engine speed, wind conditions and payload size over a period of months to detect relationships that would enable a fleet owner to run its ships more efficiently.
The business intelligence engine Caterpillar Marine developed using Pentaho gives fleet owners insight into the performance of equipment across all the ships they own. “We create our BI data cubes to map data from different sensors on ship in a way that the user can create analyzers and visualizations,” Stascavage said. “Pentaho reads the data, persists it and handles it in its own format. We create the analyzers.”
The ability to give customers these insights has enabled Caterpillar Marine to show ROI that strengthens customer relationships. It’s also yielded some dramatic examples of the impact of business intelligence.
Even small efficiency improvements can add up to big dollar savings across many vessels. Fleet owners are typically concerned with optimizing three operational capabilities: fuel efficiency, unscheduled downtime and environmental compliance, Stascavage said. Analytics has found savings in in all of those areas.
For example, some cargo boats carry up to five on-board generators to power things like refrigerators and compressors. Each of those generators may output different amounts of power so that they can be mixed and matched according to demand. For one customer, the standard operating procedure was to fire up as few generators as possible and run them at maximum speed. “You’d think operating fewer generators would use less fuel, but it turned out that isn’t always the case,” Stascavage said.
Using multidimensional analytics, the customer discovered that running more generators at lower power was more a efficient approach than maxing out a few. The $30-per-hour savings doesn’t seem like a lot, but the aggregated economies across a fleet of 50 ships operating 24 hours a day and 26 weeks a year would come to more than $650,000.
For another customer, Caterpillar Marine provided an analysis of the relationship between engine speed and the angle of propeller thruster blades. By running fuel-economy tests with blades set to different angles, and comparing that to the fuel economy of different motor speeds, the customer was able to arrive at an optimal combination of blade angle and engine speed to save about $2,200 per month per ship, or more than $26,000 per vessel per year.
Multidimensional analysis is a particularly powerful form of analytics because it enables combinations of factors to be compared in ways that wouldn’t otherwise be evident. One way in which this capability is revolutionizing the heavy machinery industry is in preventive maintenance. By combining data about operating conditions, power requirements and other situational factors, companies can match maintenance to need rather than hew to a fixed schedule.
One Caterpillar Marine customer realized fuel savings from hull maintenance planning that dwarfed the cost of maintenance. The hull of the ship takes a beating over time as it becomes encrusted with barnacles, seaweed and other ocean detritus. The resulting drag takes a toll on fuel efficiency. That much was known.
What wasn’t known was whether the cost of more frequent cleanings would be offset by fuel efficiency. The customer was spending $35,000 every two years to clean the hulls of its drive-on ships, which are used to transport vehicles. An analysis quickly discovered that dirty hulls were costing the company $1.3 million per vessel in lost fuel efficiency every two years, or over $10 million for a fleet of eight.
More-frequent cleanings were a no-brainer, but what was the optimal number? By overlaying trend lines of cleaning costs with the penalty of fuel inefficiency and identifying the intersection point, engineers arrived at an optimal schedule of six hull cleanings every two years. The result was a net cost savings of more than $800,000 per ship.
Real-time equipment predictive intelligence continues to be the company’s bread-and-butter, but multidimensional analysis powered by Pentaho is a growing part of its business. Those business insights are particularly welcomed by the fleet and heavy equipment owners who are Caterpillar’s core customers. “When they see that they’re saving money they are less reluctant to spend money,” Stascavage said.
The industrial Internet of things, combined with multidimensional analytics, “has changed the way Caterpillar Marine looks at big data,” he added. “We use ETL very heavily now. Four years ago we barely used it at all.”
Learn more about Pentaho’s data integration and business analytics solutions at pentaho.com.
Featured image by Tadek Kurpaski via Flickr CC
Other images courtesy Caterpillar Marine
THANK YOU