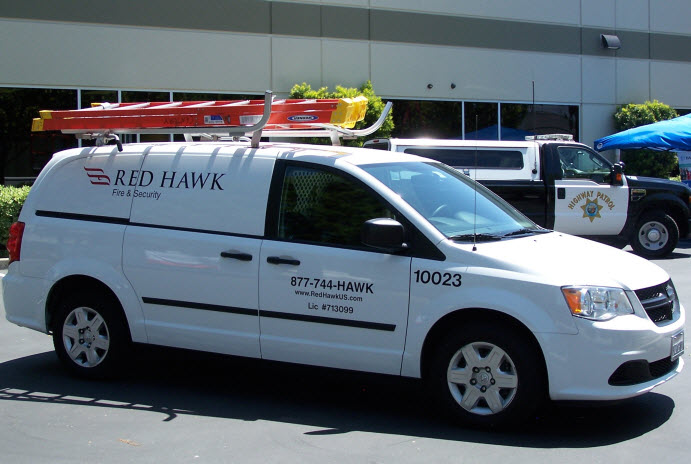
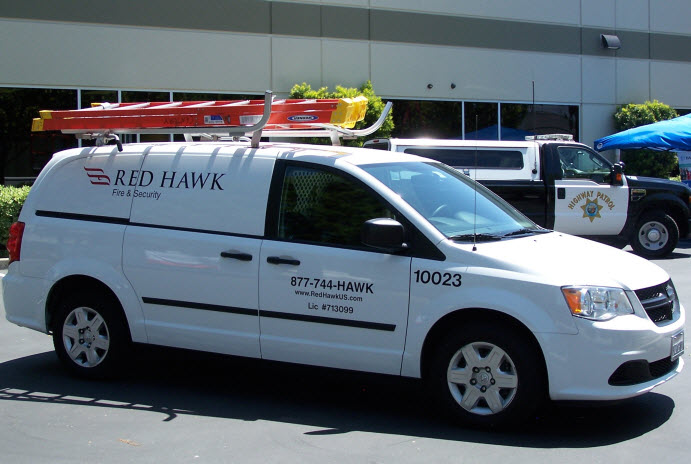
The Internet of Things may still be mostly in incubation, but in some industries it’s already mainstream. One of those is vehicle fleet management.
Operators have been using telematics and computerized engine diagnostics for years to squeeze more life out of cars and trucks while improving efficiency through route and schedule optimization. Now the same tactics are being applied to safety as well.
Red Hawk Fire & Security LLC operates a fleet of more than 800 trucks across the U.S. that attend to installation, maintenance and monitoring of its network of fire and security products and services. Three years ago, it spent nearly $1.5 million recovering from preventable accidents involving its trucks. The company figured that investing in driver education could reduce that number significantly. Then it took the next step and invested in tracking technology to verify that the training was taking hold.
Red Hawk’s fleet management services vendor, Automotive Rentals Inc. offers a unique driver safety program that combines education with electronic vehicle monitoring using telematics and GPS tracking. Drivers take a core curriculum of short online courses that address the fundamentals of safe driving. There are also modules for specific topics such as winter driving, dealing with distraction and in-vehicle cell phone use.
ARI complements its courseware with the ability to plug into the on-board diagnostic, or OBD, computers inside the engine compartment of most vehicles. Telematic devices can monitor activity such as hard braking, sharp cornering, rapid acceleration and even safety belt usage. The company also continually scans police records to catch violation reports involving drivers in its program. All this information is packaged into a dashboard that gives fleet owners detailed profiles on the skills and performance of its drivers.
“Typically, all companies can do is ask drivers to read a safety policy and sign a statement,” said Rich Radi, director of driver excellence at ARI. “We can test to make sure drivers understand it.”
Red Hawk signed on for the training program, but it added teeth to the safety initiative by outfitting its trucks with a vehicle tracking device (right) from Geotab Inc. The three-inch-long box plugs into a vehicle’s OBD port and can capture nearly anything that hits the on-board computer, including speed, fuel efficiency, RPMs, idle time, braking intensity and acceleration. It even has a motion sensor that can detect hard turns or sudden stops. All that data is packaged up for download or can be sent in real time over a cellular data network.
In essence, the company is now able to keep watch over its drivers when they’re on the road and immediately address safety issues with training or discipline.
The rollout wasn’t frictionless. The tracking device, “was Big Brother in a lot of eyes,” said Blair Schober, U.S. fleet manager for Red Hawk. “The way we handled it was to point out that we were doing this to improve customer service and the safety of our drivers. If a company is truly invested in its employees, it’s going to be invested in their well-being.”
Results came quickly. From $1.5 million in 2013, the cost of preventable accidents fell to $350,000 in 2015 and $250,000 last year. Schober estimated return on investment of 700 percent.
There have been collateral benefits as well. Safe drivers are also more efficient drivers, so fuel costs are down. By focusing on hard-braking incidents, the company has also reduced accident severity. “When I first took over health and safety, we were averaging four accidents per worker’s comp entry,” Schober said. “We’ve got that down to less than two.”
GPS tracking has also enabled the company to plan routes more efficiently and identify the closest truck in an urgent service situation. That’s eliminated the scenario in which “some drivers were traveling 30 miles to a service call and passing two other service calls on the way without even knowing about them,” Schober said.
The next step is to begin outfitting vehicles with cameras mounted on the dashboard so drivers can be observed in real time. “If there’s harsh braking or speeding, we’ll be able to look up the actual behind-the-wheel footage and review it with the employee directly,” Schober said. “We’re trying to cut that $250,000 preventable accident cost to $100,000 or less.”
And the Big Brother concerns? Well, there are no laws against a company monitoring its employees on the job. Keeping drivers safe is also a strong message. Those with the best safety records won’t be required to use dashboard cameras. The company is also tying performance appraisals directly to completion of safety training and good driving performance. Concerns about surveillance tend to go away quickly when cash rewards are involved.
THANK YOU