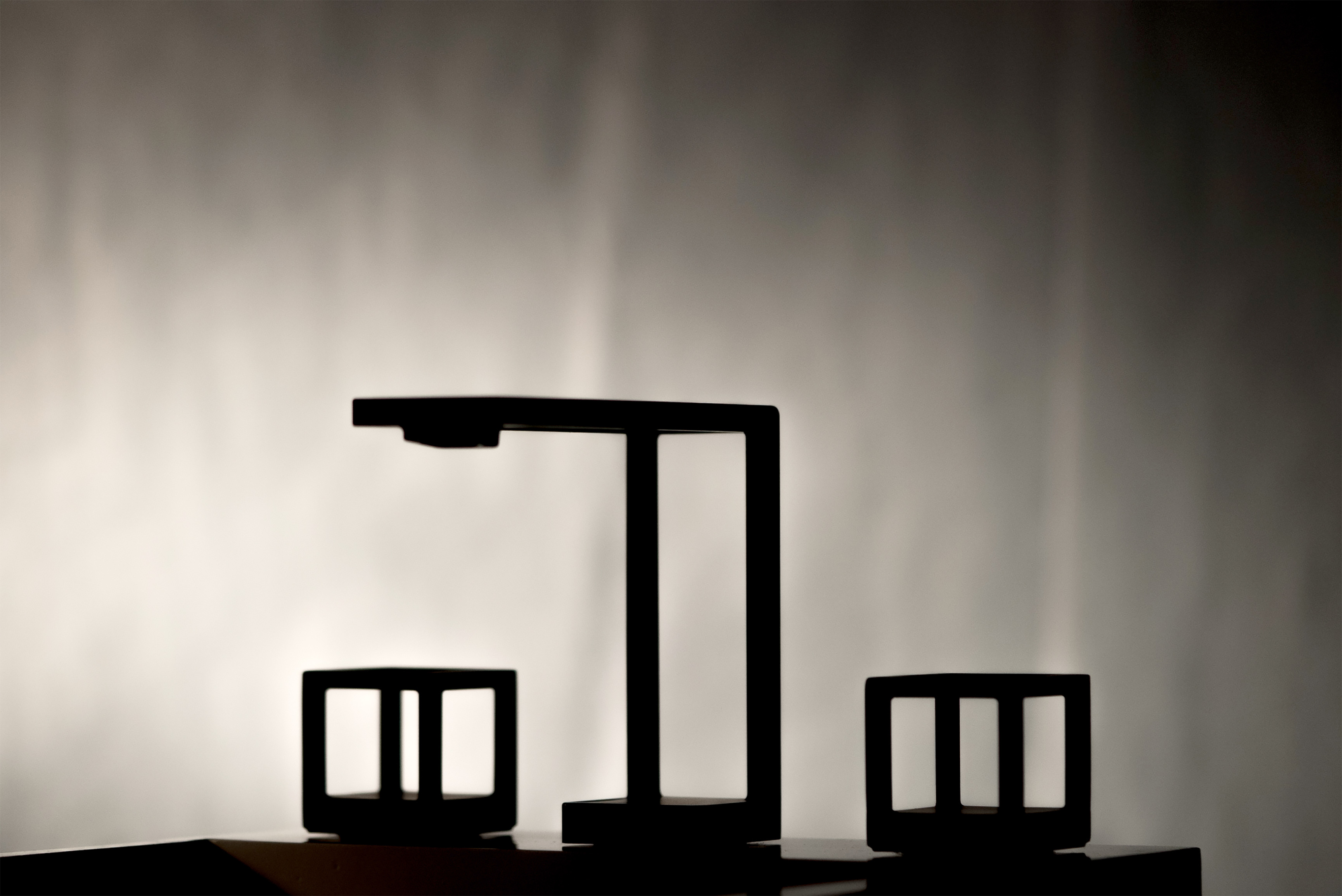
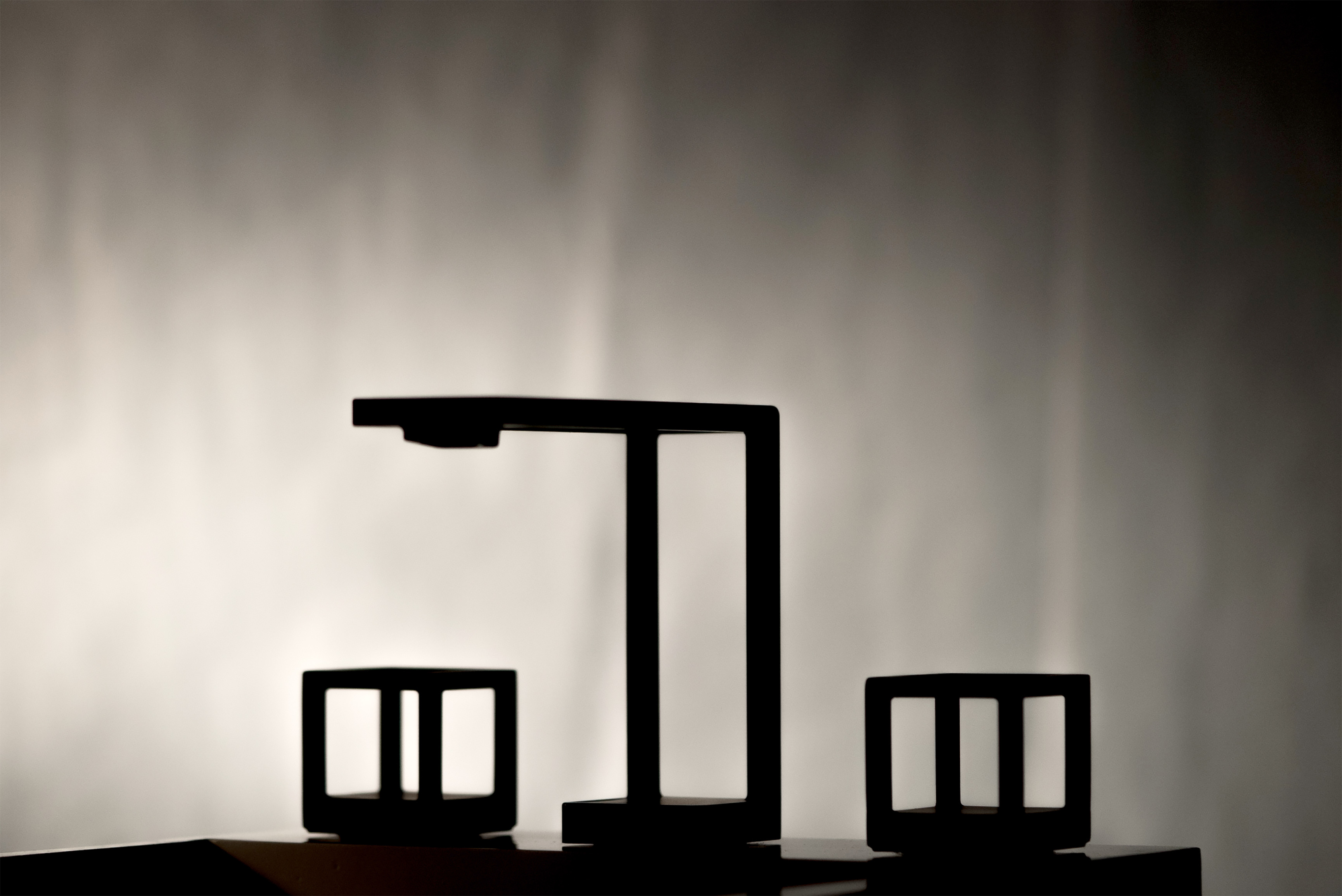
Bill McKeone has designed thousands of kitchen and bath fixtures and amassed more than 625 patents over 30 years, but until recently he was frustrated in his goal to create the perfect bathroom faucet.
Like many industrial designers, his creations have always been limited to the capabilities of the equipment needed to manufacture them in quantity. Metal molds, lathes and cutting machines can only go so far in sculpting the tiny channels and smooth curves of the ultimate water-delivery system.
Then along came 3D printing.
That gave McKeone, who’s manager of design at Kallista Inc., a luxury-brand subsidiary of Kohler Co., the opportunity to think big. Or small, in this case, because the Grid sink faucet he designed is a triumph of minimalism. “In essence, I took a form, created an outline and took away everything else,” McKeone said.
“He sketched this design pretty quickly because it’s been in his head for so long,” said Jamie Evans, Kallista’s directory of marketing.
The faucet’s unique design features handles in the shape of hollowed-out cubes, a devilishly difficult shape to make with conventional manufacturing. The waterway is only 3 millimeters wide, about the smallest possible opening through which water can pass with acceptable pressure. The faucet can thus deliver the same performance as conventional models with about half the water use – less than 1.2 gallons per minute. “There is no other faucet out there that has the waterway this small,” McKeone said.
“You would never get those kinds of waterways done in traditional manufacturing without putting together a lot of pieces,” agreed David Cullen, director of application engineering at 3D Systems Inc., the additive and on-demand manufacturing specialist that built the production plan.
The Grid is crafted from stainless steel, a material that can produce visually striking and durable products, but is also one of the most difficult metals to work with. “It wears down your cutter bits, and it’s harder to do things like threading or turning on a lathe,” McKeone said.
Using a steel powder developed by 3D Systems and the company’s ProX DMP 320 metal additive manufacturing system, production contractor 3rd Dimension Inc. isn’t encumbered by traditional production constraints. It can deliver features that weren’t even conceivable to build into a faucet a few years ago. “How do you move water through the outline of a geometric form? There was no traditional manufacturing process that could produce that,” McKeone said.
The experts are impressed. The Grid last week received the gold awards for Best in Show and Best of Bath at KBIS 2018, the kitchen and bath industry’s largest annual trade show. It was the first time a Kohler product had won the top award in the conference’s 53-year history.
3D printing is also called “additive manufacturing,” because it works by building up rather than cutting away. 3D Systems’ machines use a laser to deposit layer upon layer of metal powder on a substrate, microwelding joints only where necessary. The final product has the fewest possible moving parts and creates no waste.
In contrast, conventional faucet manufacturing involves either pouring molten metal into molds, with sand cores used to shape waterways, or cutting away pieces from a block of steel. The 3-millimeter waterways were impossible to produce with those so-called “subtractive” techniques, and the cutting process is messy and wasteful. “You try to recycle what you can, but at the end of the day you have a big pile of metal scrap,” McKeone said.
With 3D printing, manufacturing time is also quicker. Manufacturing engineers typically need six to nine weeks to design the tools and processes to put a new design into production. With 3D printing, that’s all done in software. There are no molds to crack or tools to break. Fixes or changes to the design can be put into production instantaneously.
You probably won’t find The Grid in your local big-box hardware store. It will retail for $6,995 when it goes on sale in May. For all of its flexibility, 3-D printing is still a fairly slow process. It takes about 14 hours for 3rd Dimension to produce three units.
But the technology is improving rapidly, bringing down both production time and costs. More importantly, 3D printing is enabling designers to imagine the impossible.
“The payoff is that it allowed me to accomplish the design I was after: a framed faucet with no material in the middle,” McKeon said. “Your best designs in the future will come out of these manufacturing processes.”
Support our open free content by sharing and engaging with our content and community.
Where Technology Leaders Connect, Share Intelligence & Create Opportunities
SiliconANGLE Media is a recognized leader in digital media innovation serving innovative audiences and brands, bringing together cutting-edge technology, influential content, strategic insights and real-time audience engagement. As the parent company of SiliconANGLE, theCUBE Network, theCUBE Research, CUBE365, theCUBE AI and theCUBE SuperStudios — such as those established in Silicon Valley and the New York Stock Exchange (NYSE) — SiliconANGLE Media operates at the intersection of media, technology, and AI. .
Founded by tech visionaries John Furrier and Dave Vellante, SiliconANGLE Media has built a powerful ecosystem of industry-leading digital media brands, with a reach of 15+ million elite tech professionals. The company’s new, proprietary theCUBE AI Video cloud is breaking ground in audience interaction, leveraging theCUBEai.com neural network to help technology companies make data-driven decisions and stay at the forefront of industry conversations.