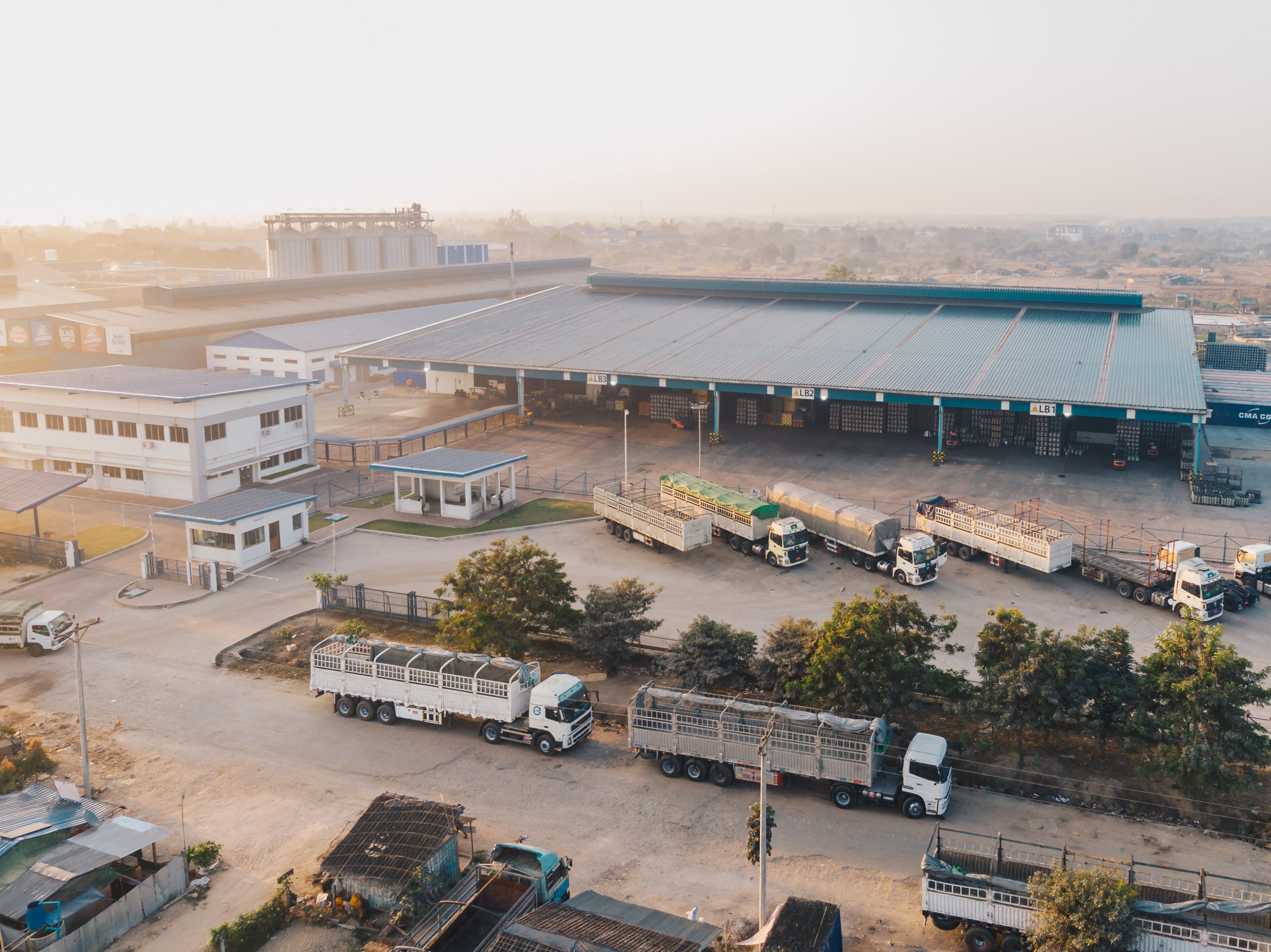
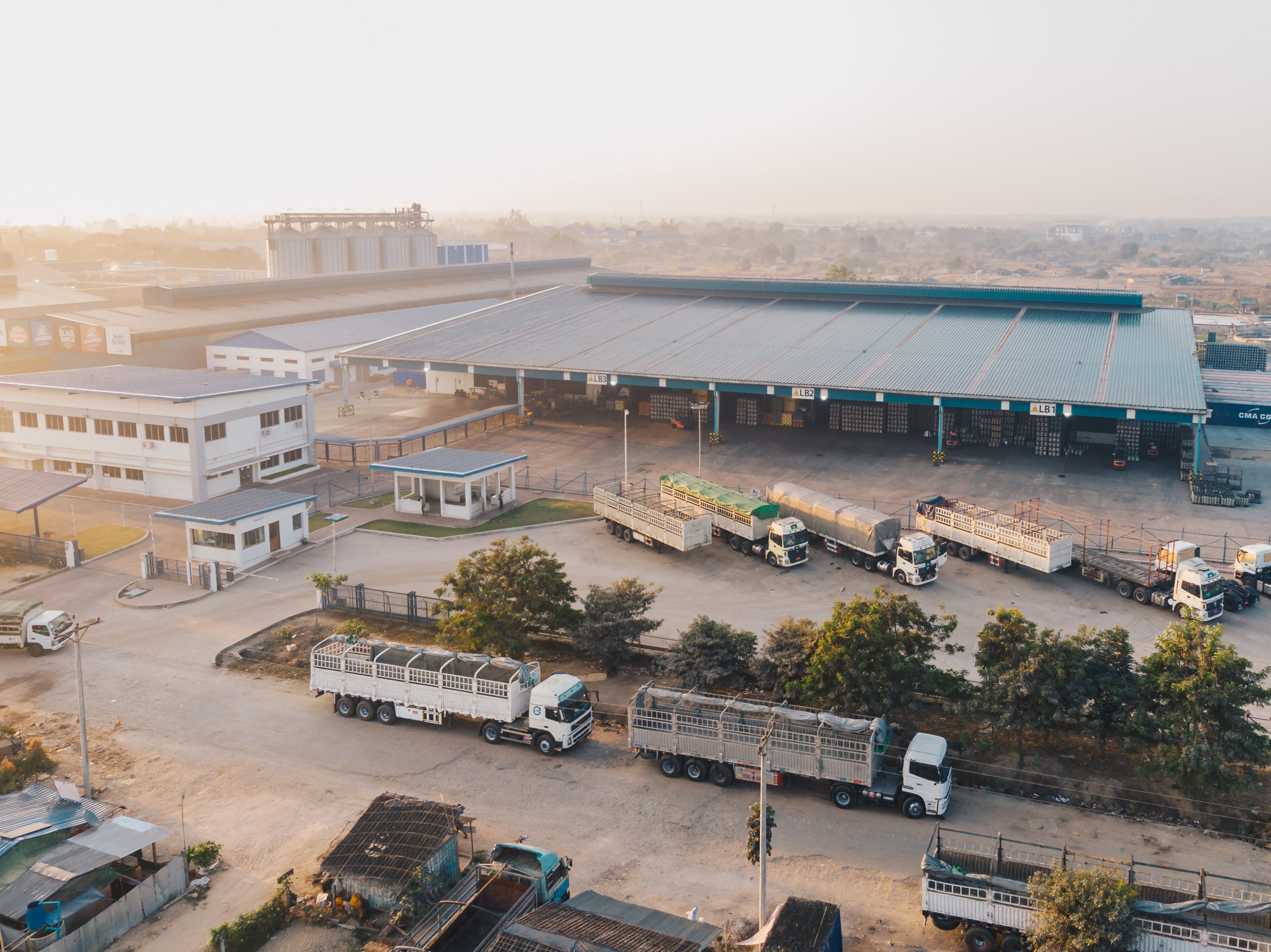
Microsoft Corp. wants to help enterprises keep on top of their supply chain management operations, so they can save on carbon emissions and ensure the kinds of global shortages of products that hit the world during the COVID-19 pandemic can be avoided in future.
To that end, the company announced the launch of the new Microsoft Supply Chain Platform today. It’s a composable platform that’s designed to help organizations maximize their supply chain data estate investments via an open approach that combines Microsoft’s artificial intelligence, collaboration, low-code and security tools.
Microsoft explained that Supply Chain Platform incorporates building blocks from Azure, Dynamics 365, Microsoft Teams, Power Platform and Microsoft Dataverse, a tool that aggregates and stores data from a range of business applications. With these tools, customers can develop a customized supply chain management platform that provides full visibility into all of their suppliers, logistics and more.
They can also develop their own custom workflows within Power Platform, and securely collaborate both internally and externally through Teams. There’s a healthy dose of analytics too, enabling companies to gain deeper insights into their supply chain and minimize its carbon footprint.
At the heart of the Microsoft Supply Chain Platform is the Microsoft Supply Chain Center, which can be thought of as a command center for supply chain visibility and transformation. It’s designed to integrate with third-party supply chain data and applications, and offers built-in collaboration, supply and demand insights, order management and other tools. Available now in preview, Supply Chain Center makes it simple for companies to harmonize supply chain data from across existing systems such as Dynamics 365 or other enterprise resource planning suites, including SAP and Oracle.
Charles Lamanna, corporate vice president of Microsoft Business Applications and Platform, said organizations today are struggling to get to grips with petabytes of supply chain-related data that sits within legacy systems, ERP platforms and other supply chain management applications.
“Supply chain agility and resilience are directly tied to how well organizations connect and orchestrate their data across all relevant systems,” Lammana said. “The Microsoft Supply Chain Platform and Supply Chain Center enable organizations to make the most of their existing investments to gain insights and act quickly.”
One of the key features within the Supply Chain Center is the Data Manager, which is used to orchestrate data ingestion so that companies can get full visibility into their supply chains at a glance.
In addition, there are a number of prebuilt modules to help customers address supply chain disruption across supply and order fulfillment. For instance, the supply and demand insights model relies on Azure AI models to predict upstream supply constraints and shortages using supply intelligence. Users can perform simulations using data provided by their supply chain network to predict stock-outs, overstocking or missing order lines. It also provides smart news insights, which deliver relevant news alerts to the Supply Chain Center on external events that might impact the customer’s supply chain.
As for the Order Management module, it can be used to orchestrate and automate fulfillment intelligently via a rules-based system that relies on real-time omnichannel inventory data and machine learning. Companies can adapt more quickly to meet future order volumes and fulfillment complexities.
Early adopters have praised the impact of Supply Chain Platform so far. Mitch Arends, executive vice president and head of operations at Kraft Heinz Co., said the platform enables it to become more agile by assessing risks and opportunities faster. “Simply put, it provides the end-to-end visibility we need to keep our products on people’s tables across North America, and there’s nothing more important,” he said.
Microsoft Teams is integrated with the Supply Chain Center, providing a way for users to collaborate with external suppliers in real time. In this way, it becomes possible to rapidly secure new supply sources, troubleshoot logistics issues and communicate upstream and downstream impacts that result from any changes.
It’s not only Microsoft’s technology, though. The company said there will also be multiple third-party modules available that will power more specific capabilities, such as Overhaul Risk Advisory Services LLC’s freight visibility solution. Because all of the data resides in a Dataverse environment, it will remain consistent for each module, Microsoft said. Additional modules are also available from the supply chain management firm C.H. Robinson Worldwide Inc., the logistics provider FedEx Corp., and other providers.
According to Futurum Research analyst Daniel Newman, supply chain solutions have become more critical than ever. “Our early assessment of the Microsoft Supply Chain Platform is that the company has put its technology, applications and resources together in a way that will serve its customer base well, offering flexibility for diverse IT environments and continuous agility for transformation in the future,” he added.
Microsoft’s partner ecosystem will play a key role in the implementation of the Supply Chain Platform, with assistance available from advisors and integrators such as Accenture Plc., Avanade Inc., KPMG International Inc. and PricewaterhouseCoopers International Ltd.
THANK YOU