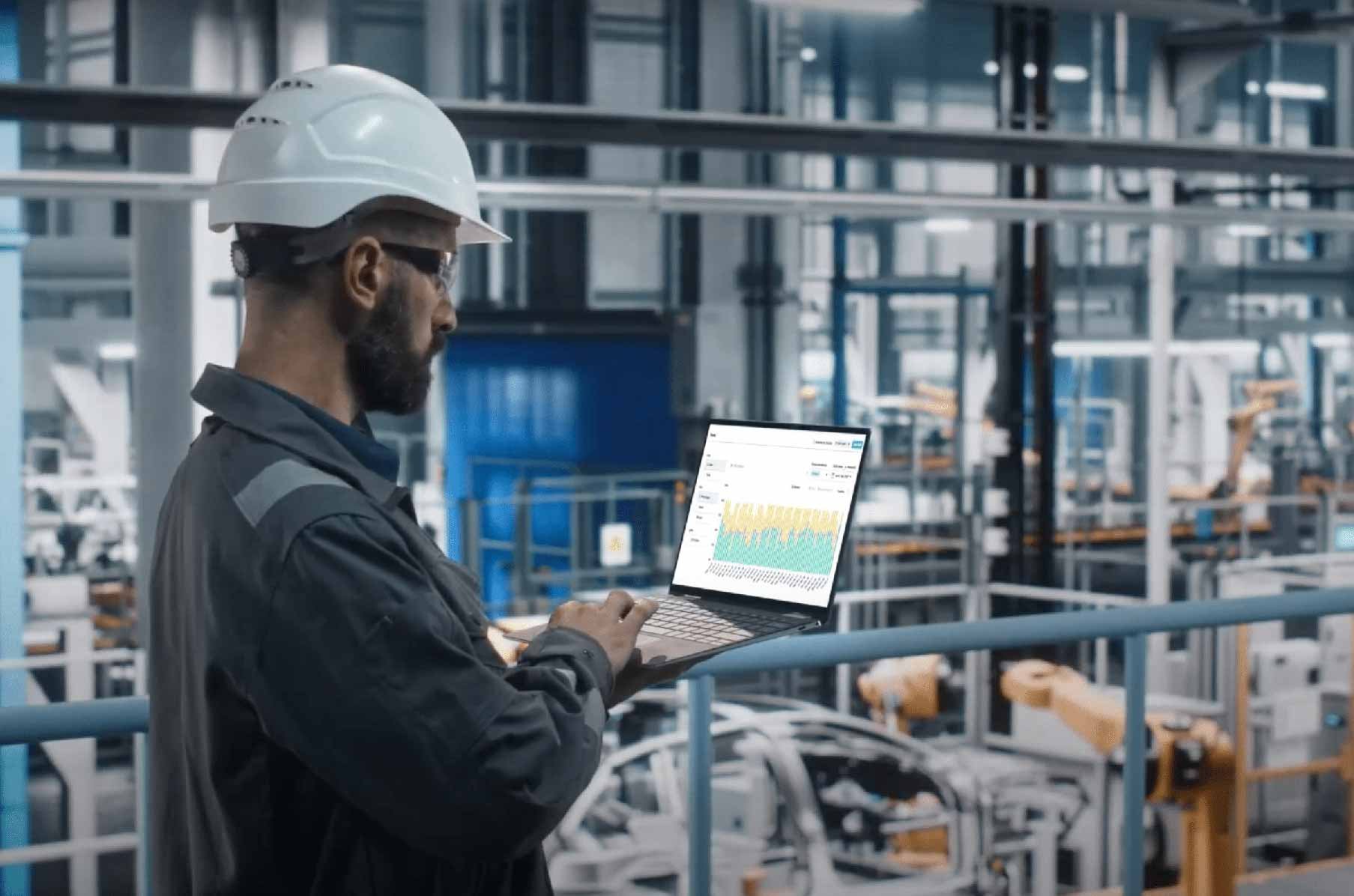
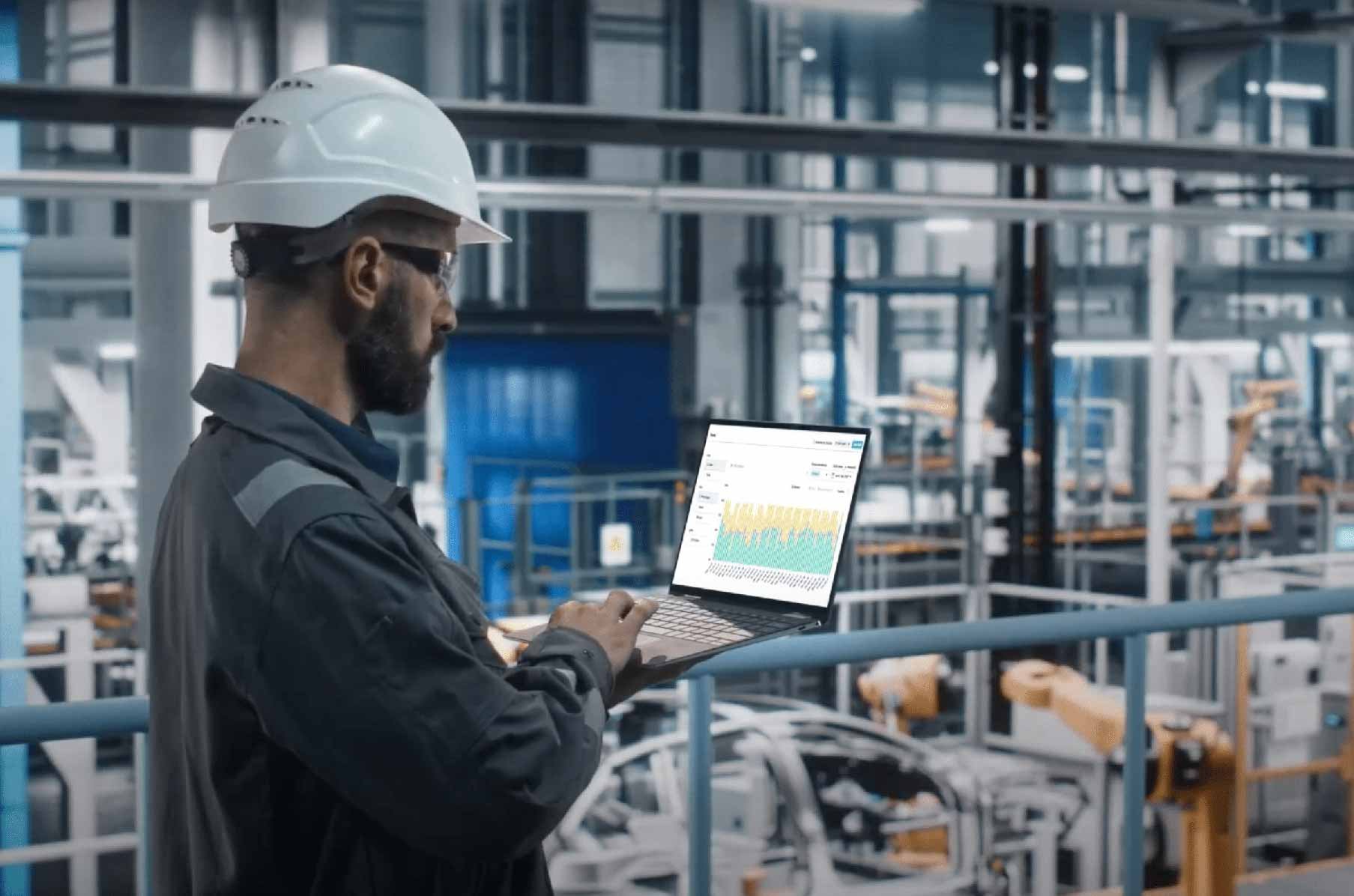
Factory software startup Guidewheel said today it’s looking to usher in a new era of artificial intelligence-powered automation for the manufacturing industry, after closing on an oversubscribed $31 million early-stage round of funding.
Today’s Series B round was led by Decarbonization Partners, which is a partnership between BlackRock Inc. and Temasek Holdings Inc. Ecolab, Rethink Impact and GSBackers also participated in the round as new investors, and were joined by existing backers such as Greycroft and Breakthrough Energy Ventures.
Guidewheel wants to streamline factory operations or “FactoryOps” by integrating AI into every machine. It’s inspired by the universal truth that every machine on the factory floor uses electrical power, and that means they can all benefit from its “non-invasive sensors” that monitor the amount of energy they use.
The startup says these sensors are used to collect data and provide insights that help factory managers to increase the efficiency and productivity of their machines and enhance performance over time.
In a blog post announcing today’s funding, Katie Doyle, head of product marketing at Guidewheel, explained that factory operators struggle to improve the performance of their machines due to a lack of visibility. That’s because traditional machine monitoring systems are extremely expensive, costing millions of dollars to install and months to get up and running, making them prohibitive for most manufacturers.
“We thought there had to be a better way,” he said. “We set out to build a solution that could be up and running in hours, would work on all machines, and would pay for itself in the first few months. This approach resonated, and today hundreds of manufacturers use Guidewheel, and growing quickly.”
Guidewheel offers what is essentially a “plug-and-play” factory monitoring system. Its clip-on sensors monitor the electric current drawn by each machine, and the information they obtain can provide useful insights into its health and productivity. This enables managers to identify the most productive pieces of equipment and their operators. In addition, changes in the amount of current a machine is drawing can signal maintenance issues that need to be addressed.
The electrical current data can be augmented by adding additional sensors for sound, vibration, temperature and pressure, in order to obtain even deeper insights.
Factory operators can progress at their own pace, the company explained, starting with the electricity sensors and progressing to the others, and over time adopt a strategy of process monitoring and predictive maintenance. Eventually, Guidewheel’s system can evolve to the point where every machine on the factory floor is fully connected, feeding data from multiple sensors to a cloud platform. Teams can then use the real-time insights they receive to head off problems, react faster to issues that need addressing and aid with operations planning.
The beauty of the system is that Guidewheel’s sensors are a one-size-fits-all solution, as they can clip onto any machine that uses electricity, regardless of what it’s designed to do or how old it is.
Guidewheel says customers quickly see a 10% performance improvement once they install its sensors and start acting on the data they provide. By implementing optimization strategies, they can increase that to a 20% performance gain over time. As an example, as machine operators become more aware of trends, they can proactively identify problems or malfunctions before they occur.
Guidewheel co-founder and Chief Executive Lauren Dunford said her company hopes to kick start a new industrial revolution on the factory floor and reshape entire business models.
“Equipment in factories often lasts for decades, and so a significant number of machines are not yet even connected to the cloud,” she explained. “Historically, the only available solutions have been cost-prohibitive and require specialized skills. Guidewheel changes that by providing a fast, scalable solution that minimizes operational disruption to swiftly connect all machines – across all ages, makes, and models – at a fraction of the cost.”
The startup boasts strong traction, with its sensors installed in the factories of companies such as General Motors Co., Igloo Products Corp., Kimberly-Clark Corp., U.S. Steel Corp., Berry Global Group Inc., Myers Industries Inc. and Johnson & Johnson Co., among many others.
Jim Campbell, CEO of Guidewheel customer Automated Solutions Inc., said he was most impressed by the fact that the software requires no programming or advanced computer knowledge at all. “Its reports and data are sophisticated and useful,” he said. “I don’t think another tool like this exists where remote, centralized support provides all of the technical expertise required.”
The funds from today’s round will help Guidewheel to accelerate product development, create new sensors and analytics capabilities, scale its AI teams and invest in its customer success teams to support its rapidly growing customer base.
THANK YOU