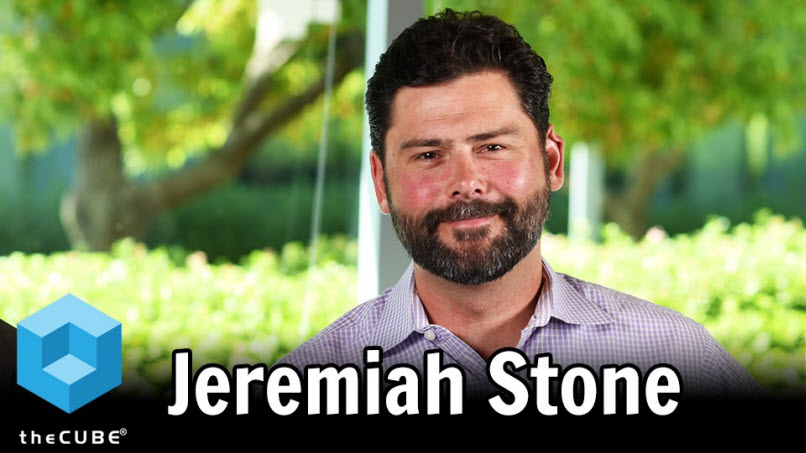
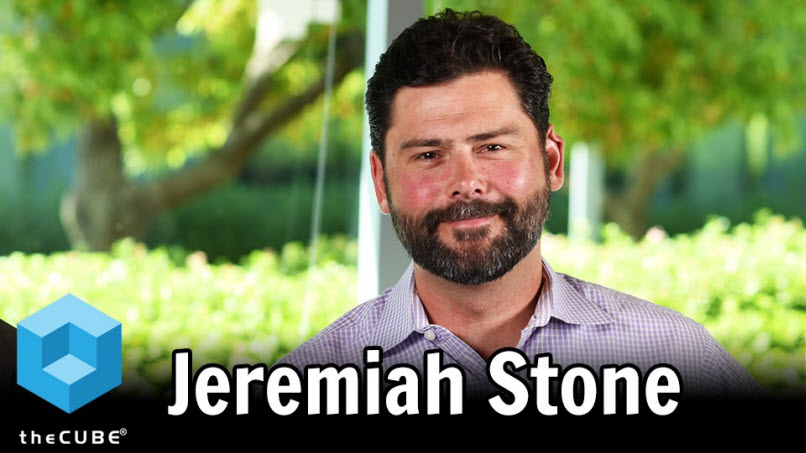
As businesses begin to connect industrial devices to the Internet in order to capture data, mine it for value and take actions based upon those insights, the task takes on almost mind-blowing complexity.
The Internet of things (IoT) is relatively simple in the context of the connected home. But industrial environments are networks of interconnected devices, each with different operating characteristics, time limitations and environmental issues. Designing a capture/analyze/respond capability has to take a multitude of factors into account that don’t exist in the home.
For example, some equipment operates at such high speed that the diagnoses and actions must be made in milliseconds, which is a challenge if the machine is located in the Alaskan tundra. Maintenance applications need to take into account the fact that some equipment is non-essential enough to be able to survive a total failure, whereas other machines are so critical that failure isn’t even an option.
Other interviews in this series
GE Predix chief architect sees IoT analytics as a game-changer
How GE Predix tackles the unique challenges of the industrial IoT
GE’s Predix: designed for analytics when milliseconds matter
And when that equipment is 1,000 miles from civilization, failures must be anticipated days in advance to enable repairs. Critical infrastructure equipment – such as that involved in the operation of a power grid – can’t be connected to the public Internet because of security concerns. And there’s the overarching fact that much of the equipment that industrial companies are trying to instrument now was never meant to be connected in the first place.
These are some of the problems that Jeremiah Stone (@jeremiahstone) and his team at General Electric Co.’s Predix business unit tussle with every day. Stone, who is general manager of asset performance management at GE Digital, recently spoke with theCUBE’s Jeff Frick (@JeffFrick) at GE Digital’s Innovation Day 2016 about the complex problems GE engineers are solving as the Internet of things moves into the industrial mainstream. (*Disclosure below.)
IoT will enable unprecedented productivity gains in some areas because of the sheer speed of computers and networks. For example, the process of milling platinum requires a precise configuration of machinery that must be changed frequently to maximize yields. Analytic algorithms can manage those changes much faster than humans ever could, Stone said, thus avoiding the risk of “throwing stuff in the trash that could be platinum,” as is sometimes necessary today.
IoT will reduce waste is by throwing off precise information that can be used to diagnose and repair equipment, improving efficiency. For example, solar power equipment is devilishly expensive to service. For one thing, it’s usually sited far away from urban areas. Specialized skills are also needed to maintain it, and the process is subject to regulatory scrutiny and security concerns. “You’ve got to be able to make a change without having to re-permit the entire facility,” Stone said. Sensors will enable solar equipment operators to diagnose precisely when and where repairs need to be made so they can dispatch service people with the right skills at the right time, preventing failures and lowering service costs.
GE created Predix because the company believes it is uniquely well-suited to provide the kind of diagnostic and operational capabilities that industrial customers demand. GE has more than 60 centers around the globe monitoring more than $1 trillion worth of equipment. “We have decades of experience connecting to machinery, providing advanced control systems and bringing that data back for analytics,” Stone said.
Part of the complexity of industrial environments comes from simply determining where to locate intelligence, whether in the cloud, on local controllers or within sensors themselves. “It’s a network, not a hub-and-spoke,” Stone said. Another complicating factor is that large machines, such as locomotives and airplanes, carry a lot of different equipment from different companies. Getting those machines just to talk to each other is a challenge in itself. Making sense of what they’re saying is even harder.”
GE starts by looking at desired outcomes and works backward from there in order to simplify scope. For example, “Will the outcome be physics-based analysis, such as understanding metallurgy? Or will it be statistical, such as using machine learning methods to identify and understand something that you can’t do otherwise?” Stone said. said. Narrowing down desired outcomes reduces complexity. “It’s not about big data; it’s about correct data.”
The business and regulatory environment also influences choices. Customers in regulated industries, such as utilities, are pushing to tightly integrate computing with the assets being managed. That’s because exposing data on a public network or cloud could have disastrous security consequences. On top of that, “Operators in different parts of the world have different regulatory environments,” Stone said. “We need to be very adaptable. It all comes back to understanding business cases.”
It also means bringing together IT and operational experts to determine what data matters and how it should be gathered and analyzed. Collaboration yields exciting breakthroughs, Stone said. “Knowing that a transformer is near the end of its 70-year life out in the middle of nowhere, and that you can get 10 more years out of it is only possible if you take a data-driven approach,” he said. “You need to know how to operate the machinery and also how to apply the data.”
That’s why GE is doing a lot of work with artificial intelligence and machine learning to apply statistical principles to the data its customers gather. “What’s exciting is when we discover a low-cost, feasible way of doing something that couldn’t be done before, and we can roll it out at scale,” he said.
Like the recent discovery by one GE data scientist of a way to help an airline customer wring a two percent productivity boost out of its supply chain. “A couple of percentage points at scale makes a big difference,” Stone said.
Watch the full interview below (25:39).
* TheCUBE, owned by the same company as SiliconANGLE, was the paid media partner at GE Digital’s Innovation Day. Neither GE nor other participants have editorial control over content on theCUBE or SiliconANGLE.
Support our open free content by sharing and engaging with our content and community.
Where Technology Leaders Connect, Share Intelligence & Create Opportunities
SiliconANGLE Media is a recognized leader in digital media innovation serving innovative audiences and brands, bringing together cutting-edge technology, influential content, strategic insights and real-time audience engagement. As the parent company of SiliconANGLE, theCUBE Network, theCUBE Research, CUBE365, theCUBE AI and theCUBE SuperStudios — such as those established in Silicon Valley and the New York Stock Exchange (NYSE) — SiliconANGLE Media operates at the intersection of media, technology, and AI. .
Founded by tech visionaries John Furrier and Dave Vellante, SiliconANGLE Media has built a powerful ecosystem of industry-leading digital media brands, with a reach of 15+ million elite tech professionals. The company’s new, proprietary theCUBE AI Video cloud is breaking ground in audience interaction, leveraging theCUBEai.com neural network to help technology companies make data-driven decisions and stay at the forefront of industry conversations.