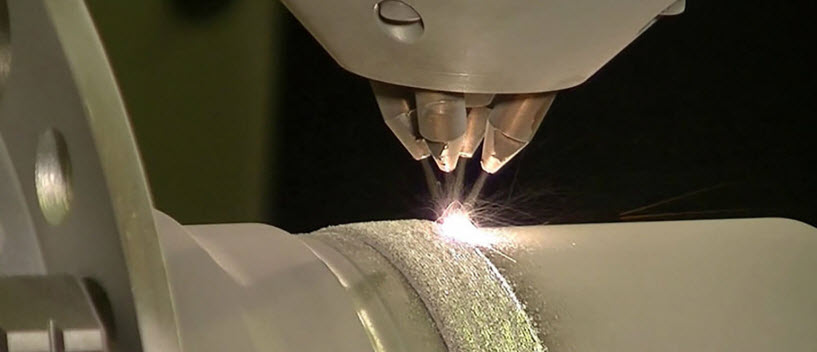
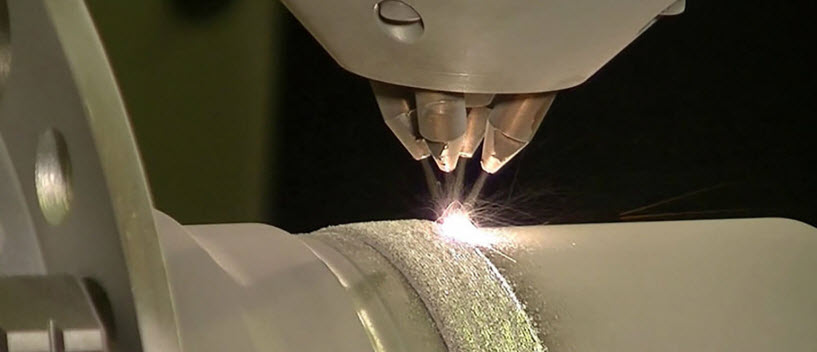
The New York Times once described Duann Scott (@Duanns, below right) as “a Pied Piper for on-demand 3-D printing,” an analogy that pretty well sums up what Scott has been doing since he relocated to New York from his native Australia six years ago. In his prior role as a designer evangelist at Shapeways Inc., a contract 3-D printer and retailer, Scott promoted the value of 3-D printing – also called “additive manufacturing” – as a way to help designers manufacture things that are impossible or impractical to build with conventional toolsl and techniques. Since joining Autodesk Inc. in 2014, he has directed business development and strategy for Autodesk’s Digital Manufacturing Group, which is building partnerships with industrial firms and investing in 3-D-related technologies. Autodesk has set aside $100 million to spur 3-D printing innovation.
SiliconANGLE caught up with Scott for a phone interview about the latest developments in his field of expertise.
An article in TechCrunch recently asked Whatever happened to 3-D printing?, implying that the technology has under-performed its potential. Do you agree?
The idea of a 3-D printer in every home was never realistic. These printers are powerful tools for design engineers to quickly iterate on a design, but they’re really not suitable for people who can’t design. It can take three hours to print a door wedge. The cost of the material and time far outweigh what you can get at the hardware store for two dollars. Shapeways did see some traction around jewelry, but when it comes to something like an iPhone case, it’s cheaper and more durable to find something that’s mass-produced.
What are some common misperceptions about 3-D printing?
The most common is that it’s a black box where something magical happens. In reality, there’s usually a lot of post-production that goes into making a part produced on a 3-D printer ready for use. Many people also expect the process to be fast. Compared to standard prototyping it’s rapid, but it isn’t the instant gratification of downloading from an app store. Plus it takes time and effort to maintain the machine.
It’s critical that machines, materials and software are developed in conjunction to make sure they all work together. At the moment, most people are designing something and throwing it at a machine. That doesn’t work. Materials and design companies need to work together to make sure they maximize the value of the technology.
What will the role of recent patent expirations play in the evolution of this technology?
Additive manufacturing has been around for 25 years purely for industrial uses. Machines were expensive and materials were controlled by manufacturers. When those patents expired we saw prices come down from $35,000 to $200. A lot of the key patents are now expiring for other technologies. Fused deposition modeling (FDM) is one of them. We saw an explosion of new machines when prices dropped.
Another is selective laser sintering (SLS) for laser printing with nylon powder. That patent expired a couple of years ago. We will see machines coming from China and Europe that will take the costs down from $500,000 to $7,000.
Why is nylon powder important?
Traditional injection molding has something like 130,000 materials. With 3-D printing there are currently about three. Shoe makers want to use this technology to customize shoes, but they weren’t able to get the materials they require. Now that these patents have expired, we can see third-party tool makers start to enter the market and offer more materials, which will lead to more uses.
For example, the powder bed 3-D printing patent is expiring. That’s a way to glue powder together that’s useful in visual prototyping. This will allow other machines that work with materials such as concrete to enter the market. A U.S. company called ExOne [Co.] uses a similar process with stainless steel to print bronze alloy parts.
Where will biggest short-term impacts of 3-D printing be?
Where 3-D wins is in areas where things need to be customized, so you’re seeing it really catch on in medical and dental use. Invisalign [from Align Technology Inc.] is the most successful 3-D printing company in the world. There’s something on the order of 15 million 3-D hearing aids in the world, because they need to be customized to the individual.
Another area is where there’s a lot of effort involved. The poster child of that is GE’s fuel nozzle. The part itself isn’t complex but the assembly is. And in the metals area you can make engine parts that dissipate heat in ways that aren’t otherwise possible.
What recent advances excite you most?
Multi-material, where you can print both a polymer and conductive material to create complex products. At the moment it’s used primarily in defense, but it can quickly go into consumer products. I can see complex medical parts and things with lots of antennas. Only a few things we own are made from one material. Once you have multi-material printing it changes everything.
There are also hybrid processes emerging with a mix of additive and subtractive techniques. So you can use additive processes to fill in the part of a turbine that’s wearing and subtractive processes to finish it within one machine.
How about in consumer world?
The idea of having a UPS store with the 3-D printer for spare parts makes good sense. You can have a digital archive of replacement parts and print them on demand with a verified source. That has a lot of potential.
THANK YOU