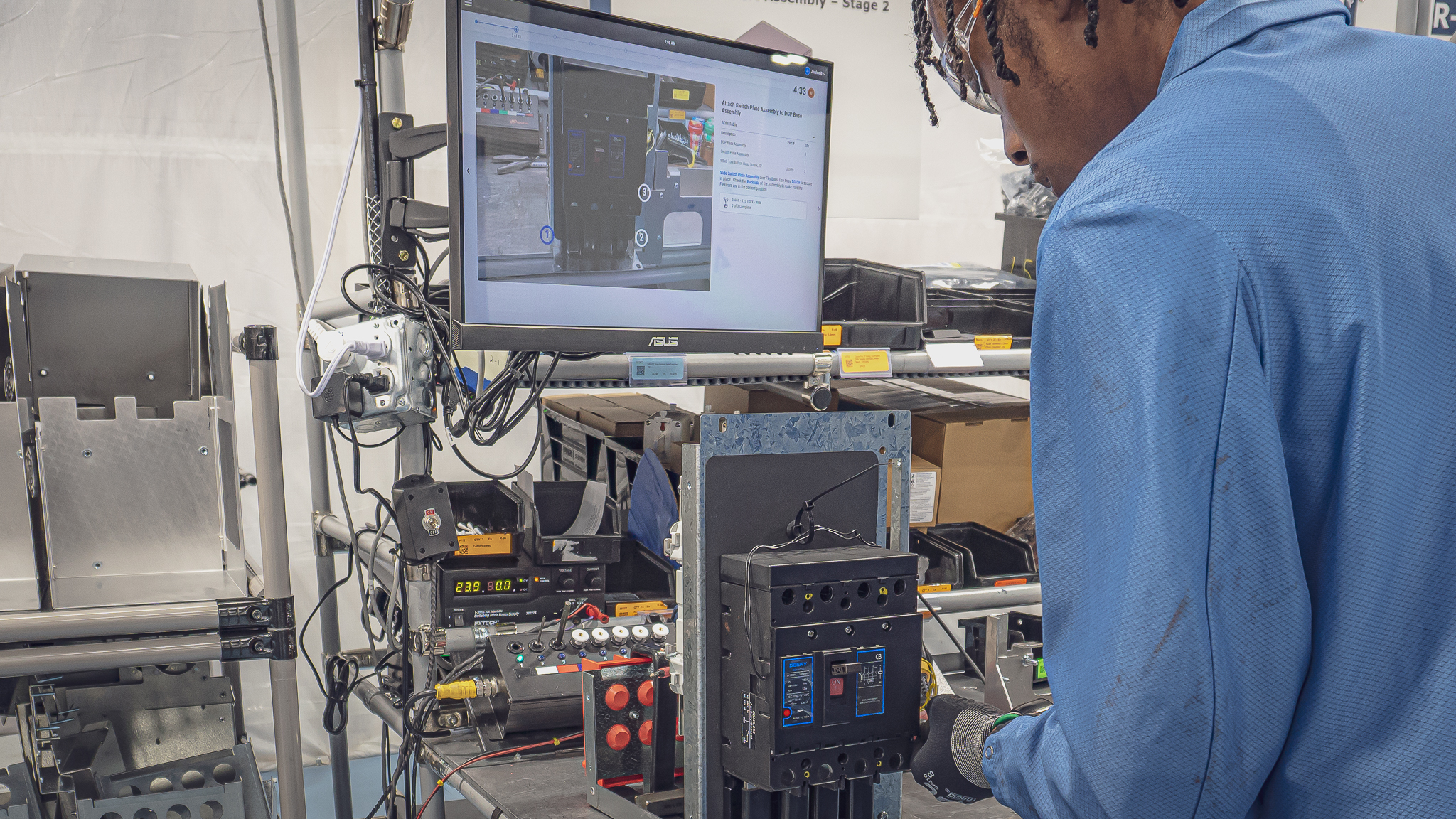
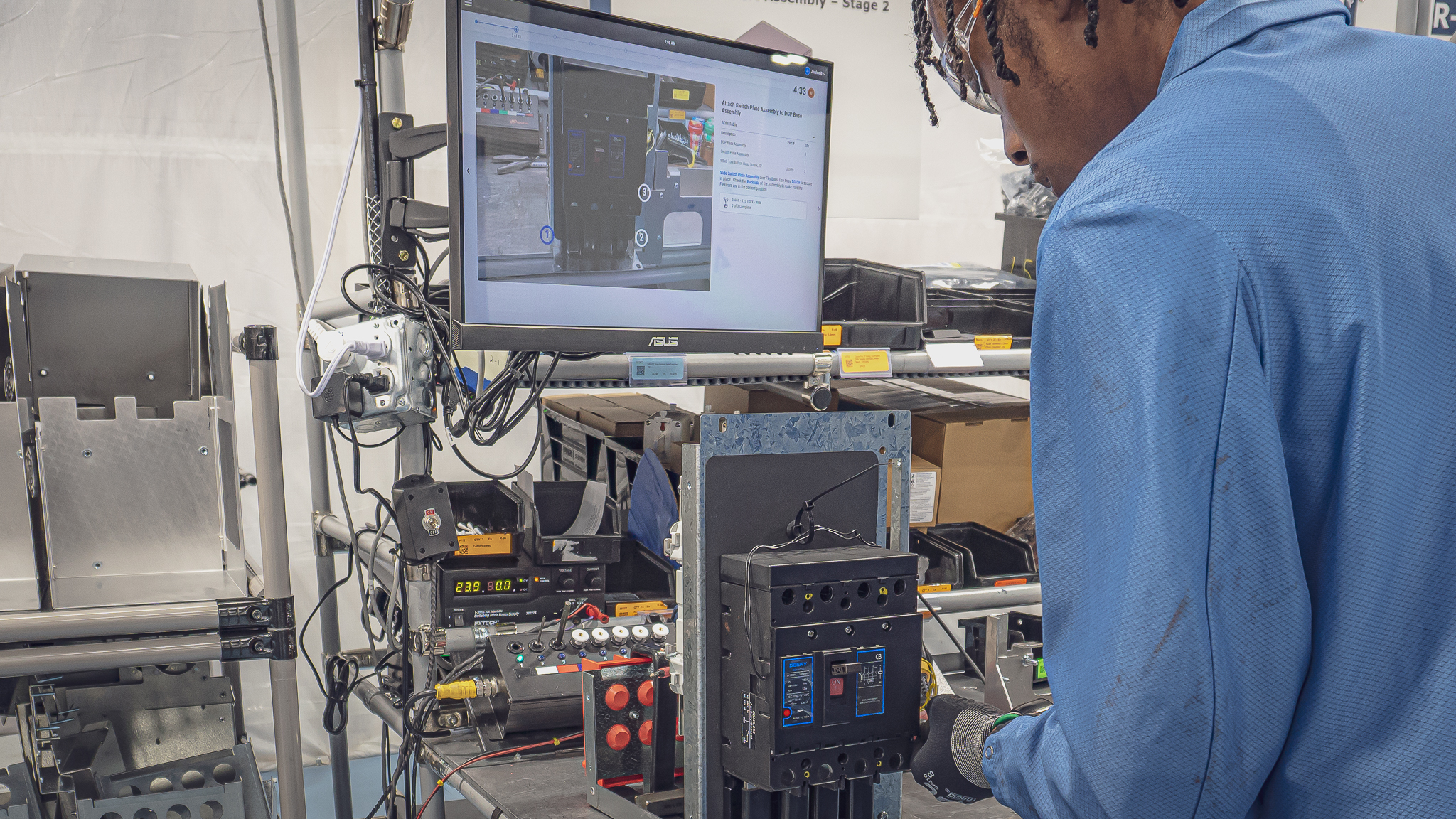
Pico MES Inc., a software company that helps small and midsized manufacturers better manage their factory floors, today said it has raised $12.35 million early-stage investment round, bringing the company’s total funding to $20 million.
Participants in the Series A round notably include the venture capital arms of two large manufacturers: Bosch GmbH and Schneider Electric SE. Other participants include Counterpart Ventures LLC, Momenta Ventures AG, Lemnos Labs Inc., Congruent Ventures LLC and Union Labs Ventures LP.
Pico sells as an edge-based hardware/software manufacturing execution system that collects data from thousands of devices used in manufacturing, ranging from torque wrenches to bar-code scanners. It then analyzes it to help factory managers streamline workflows and troubleshoot productivity and quality problems. Its platform combines a local computer with back-end connections to cloud storage and analytics software and an open application programming interface can be used to connect to most shop-floor systems.
Small and midsized manufacturers have largely been ignored by manufacturing resource planning and factory automation software makers despite the fact that they constitute 98% of all U.S. manufacturers, Pico said. Most of those companies still use paper and spreadsheets to track and measure operational efficiency, according to Pico’s internal research.
“We try to answer three questions that every factory owner asks: What did I make? How much did it cost me to make it? And what did I pay people to do?” said Ryan Kuhlenbeck, co-founder and chief executive officer of Pico. “We put the power back into the shop floor teams to not only set up their systems but also to see results and take action without having to go pay somebody to make a change.”
The product’s connection to 150 families of tools – each with between 50 and 100 different models – “is the most comprehensive library of its kind on the planet,” he said.
Pico MES can process real-time data to prevent quality defects on the floor and conduct batch analytics in the cloud to improve efficiency. “When you’re assembling a battery pack and a high-voltage connection is not properly torqued, bad things happen,” Kuhlenbeck said. “We can allow a battery maker to implement a connected torque tool within five minutes so that instead of counting on the operator to never make a mistake, the tool can tell you exactly what the torque levels are. It cannot be bypassed.” Workflows can be orchestrated to prevent an item from proceeding to the next step in the manufacturing stage unless the preceding stage was completed successfully.
Data gathered from microcontrollers serves a web application that lets operators see a real-time data feed of how systems are operating. A drag-and-drop workflow builder enables manufacturing engineers to map sequences of events and track in real-time how well assembly lines perform compared to expectations.
“We can infer from that workflow all the information necessary to give the customer full traceability,” Kuhlenbeck said. “Here is exactly how your part was built, not how you think it was built.”
Lithos Energy Inc., a 65-person San Rafael, California-based maker of lithium-ion batteries, has seen defect rates drop by more than 30% since it adopted Pico MES three years ago, according to James Meredith, the company’s president.
“You can’t ship a battery unless you have 100% certainty that bolts and joins are seated correctly,” he said. Lithos’ manufacturing process is programmed into Pico MES and workflows are tied to specific quality metrics.
“When you shoot a screw or a nut, the tool is counting turns, measuring torque values and communicating when those values are hit,” Meredith said. “The tools at the subsequent stations won’t accept a part until that torque value is hit. The system is locked up until you finish the required task.”
Lithos has also been able to improve efficiency by identifying bottlenecks in the manufacturing process. “We can look at the station where things are getting stuck or a lot of people doing rework,” Meredith said. “If the station has been locked for 15 minutes, we want to know what’s going on. This directs us to the areas that need improvement.”
Thanks to a recent investment from Caterpillar Inc., Lithos is preparing to move into a new 65,000-square-foot facility. Meredith said Pico’s software has helped burnish the company’s reputation as a high-quality provider.
“There’s nothing quite like it,” he said. “Pico has been a sea change for us and we’ve been able to implement it very rapidly and easily.”
THANK YOU